The following is an article found in PRSM Magazine in their 2015 March-April issue. It was written by Brian Bourque with quotes from Bill Pegnato.
It’s an often repeated story, back in the 80’s when insulating contractors discovered the water repellant qualities of sprayed-on polyurethane, they suddenly found their way onto the tops of commercial buildings, spraying foam. But without the prerequisite knowledge of roofing systems, in too many cases, installers produced substandard work.
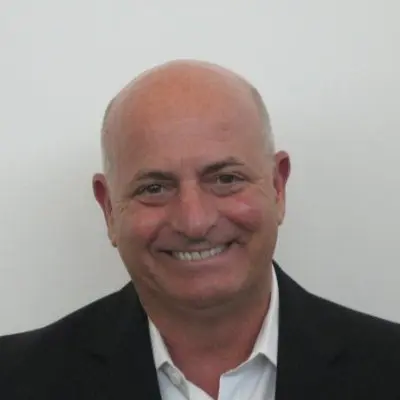
According to Bill Pegnato, of Building Power, LLC, the story has some validity and explains that when spray foam was introduced for roofing applications much of the work was being done by installers who didn’t know enough about roofing to achieve adequate results. “They were basically insulation contractors, and although they understood the foam material was waterproof, their application techniques were sometimes faulty. One of the most common mistakes occurred in their lack of preparation of the existing surfaces, resulting in botched jobs that unfortunately tainted the reputation of spray foam products.”
Over time, that’s changed, Pegnato says, and the industry is delivering good results with SPF, “In general spray foam roofing systems are a great choice for the right application.”
One case in particular, says Pegnato, came recently when a large box clothing retailer in Tampa, Florida needed a replacement for an old, coal tar build up roof. “It was at the end of its life and needed replacing. To replace the roof the specification called for removal of the old roof, a costly piece of the overall estimate. And to make matters worse, after work had begun, we realized there was a drainage problem caused by deck deflection worse than anticipated. This new piece of information had the potential to increase the costs dramatically.”
In this instance, Pegnato said the specification was rewritten to deploy a foam system. The benefits were clear, in this case he said. “Using foam allowed us to avoid a tear off of the old coal tar pitch roof. The original TPO specification required a tear off as the fasteners penetrating the deck would allow the coal tar to seep into the space. Not only is this economical, it’s an eco-friendly practice as we do not need to dump the coal tar in a land fill. And since the foam is self-flashing and self-tapering the application can allow for proper drainage. And finally, it’s less costly overall than the original spec. In this case we experienced the perfect application for a foam roof installation.”
Generally speaking, Pegnato says foam roofing systems are relatively easy to restore with coatings so they can literally be maintained for the life of the building. Additionally, for buildings in warm climates, foam increases the r-value of the typical roof, requiring less energy to cool the store.
Pegnato recommends, as is the case with all re-roofing projects, to start with a quality manufacturer of the system you will be installing. Work with the manufacturer to match product information to your needs and to obtain a short list of contractors they certify to install their product.
“Do your due diligence, seek out qualified manufacturers and certified contractors. At that point you are dotting you i’s and crossing your t’s,” Pegnato concluded.
Brian Bourque is Director, Communication & Public Relations at PRSM Association. He can be reached at bbourque@prsm.com.