The following post is a memo written by Rich Allen, MBA, CHSP, CES, IRC Safety Director on May 16, 2016.
In November 2012, the National Institute for Occupational Safety & Health (NIOSH) a sub-division under the Center for Disease Control (CDC) published an Alert titled Preventing Occupational Respiratory Disease from Exposures Caused by Dampness in Office Buildings, Schools and Other Non-industrial Buildings. This alert was published regarding Sick Building Syndrome and Mold Due to Leaking Roofs
In the Alert NIOSH defined “dampness” as the presence of unwanted and excessive moisture in buildings that can lead to the growth of mold, fungi and bacteria, and to the breakdown of building materials. NIOSH further used the term “mold” to define a group of fungi common in wet materials.
Risks of Moisture in Your Building
Research studies have shown that exposure to these molds and building dampness has been associated with respiratory symptoms, asthma, hypersensitivity pneumonitis, rhinosinusitis, bronchitis, and respiratory infections.
Children tend to be more susceptible to these illnesses. This can be prolonged or aggravated through lack of knowledge and understanding of the nature or severity of the problem. Suboptimal design, construction, and commissioning of the building may create the problem in new building construction. Once constructed, dampness issues can develop due to improper maintenance and upkeep of the facility. Deterioration of roofing and window seals is the number one cause followed closely by poor maintenance of Heating, Ventilation and Air Conditioning (HVAC) systems.
Detecting Moisture
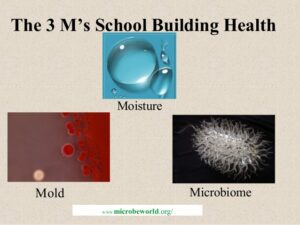
NIOSH suggests that the best evidence is observations of dampness, water damage, mold and mold odors in the building. These observations give building owners, employers, and occupants indications of dampness-related health hazards. The following actions are recommended for addressing persistent building dampness and subsequent respiratory problems in exposed occupants.
- Respond when occupants report health concerns.
- Regularly inspect building area such as roofs, ceilings, walls, basements, crawl spaces and slab construction. Take prompt action to identify and correct any occurrences of dampness.
- Inspect roof systems to determine if in good condition.
- Are there signs on the roof of upper layers delaminating or pulling away?
- Are there rips, tears or detached seams?
- Is roof free of pooling water?
- Is roof draining properly to drains and scuppers?
- When looking at ceiling or decking and inside exterior walls and windows, are there water stains or streaking?
- Conduct regularly scheduled inspections of HVAC systems and promptly correct problems
- Dry any porous building materials that has become wet from leaks or flooding within 48 hours.
- Clean and repair or replace building materials that are moisture damaged or show signs of visible mold growth.
- Inform occupants that respiratory effects from exposure to damp buildings can cause respiratory illnesses and encourage them to seek medical attention if they develop worsening or persistent respiratory problems.
Enacted Standards
Over the past decade, federal OSHA has proposed standards for Indoor Air Quality to deal with issues of indoor moisture and associated microbial colonization. However, the standards have not been enacted. While waiting for federal OSHA standards to be enacted, several states have enacted their own versions of the law. California, Maryland, Massachusetts, Montana, New Jersey, North Carolina, Virginia and Washington all have laws dealing with workplace exposures to indoor dampness.
In 2012, the American Society of Heating, Refrigeration and Air-Conditioning Engineers (ASHRE) published a position paper titled Limiting Indoor Mold and Dampness in Buildings. Although much of it had to do with HVAC maintenance and design, they also spent considerable time discussing the need for proper maintenance and upkeep of roofing systems and flashings. The bottom line in their position paper was that no matter how good the HVAC system is it can’t compensate if you can’t keep the water out.
Case Study
In April 2011, employees of a Florida accounting office requested a health hazard evaluation to investigate concerns of indoor environmental quality. Employees requested the audit due to headaches, fatigue, weakness, fever, chills, flu-like symptoms, shortness of breath, coughing, chronic sinusitis, sore throat, and burning eyes. NIOSH performed the assessment on June 22 – 23, 2011. NIOSH found:
- ill-fitting weather strip on exterior doors,
- water-stained ceiling tiles, window sills and walls
- raised area on cloth wallpaper from previous water leak
- rust stains at roof lap joints
- musty odor at 2 air-handlers, dust accumulation and visible mold on the roof
- water stains on a wall from a reported roof leak
- ponding of water on a deteriorated section of the roof near a drain
- plant growth on the roof
This assessment and its findings underscored the need for routine inspections and proper repair of roofing and HVAC systems.
Support for New Standards
The Building Owners and Managers Association International (BOMA), who supports consensus-based codes and standards, believes that mold is an ever-present fact of life and can be found both outside and inside of structures. Without moisture, mold has no opportunity to develop. Moisture can be caused by high humidity, dripping pipes and leaky roofs.
According to the EPA, mold can begin growing in 24 to 48 hours, so it is important to dry water-damaged areas as quickly as possible to prevent mold growth.
BOMA recommends the best way to prevent most indoor mold cases is through an effective inspection, maintenance, and repair program by building owners.
In 2006, OSHA published its guide – “Preventing Mold-Related Problems in the Indoor Workplace – A guide for Building Owners, Managers and Occupants.” This 32 page guide echoes the same themes highlighted above, though it came out several years prior to EPA, BOMA and NIOSH documents.
It is interesting to note that OSHA originally proposed their Indoor Air Quality Standards in the 1990s but was not adopted into law at that time. The majority of this proposed standard dealt with smoking habits of the occupants. As no Federal Standard exists today, in the 2006 document, OSHA alludes that these issues could be cited under the General Duty Clause.